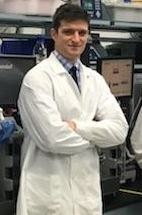
Mathew Halter
The joint venture of DuPont and Tate & Lyle has developed a proprietary process that uses plant-based instead of petroleum-based feedstocks to produce 1,3-propanediol. Today, the company provides solutions for a wide variety of markets and applications through its bio-based performance brands Susterra® and Zemea® propanediol in addition to Bio-PDO™, the key ingredient for DuPont™ Sorona® high-performance polymers. DuPont Tate & Lyle recently announced an expansion to their manufacturing facility in Loudon, Tennessee, toff increase annual production of bio-based 1,3-propanediol by 35 million pounds by mid-2019. Mathew Halter, Molecular Biologist responsible for Bio-PDO Strain Development at DuPont Tate & Lyle Bio Products, offers his view on the future of renewable materials:
What are your thoughts on the future of renewable materials?
As global demand for raw materials increases, the ability to provide everyday products from renewable and sustainable sources is going to become more and more important, not only environmentally, but competitively, as well. Yes, there are major environmental incentives to becoming more sustainable, but in a global market that is going to rapidly change in the next decades in a move towards providing for many more with far less, it will not only be environmentally necessary, it will be economically necessary.
What innovations do you expect to see in renewable materials?
With new White Biotech target molecule processes constantly being developed across the globe, I would say that the metabolomics and biochemistry behind these new pathways are not so much innovations as inevitable checkpoints. I think the main innovations in the field will come in feedstock development, allowing more complex processes to take place utilizing cheaper and “dirtier” feedstocks such as lignocellulosic, gas byproduct emission and trash combustion emission feedstocks. The foundation for the metabolic engineering of pathways to produce traditionally petroleum-based molecules from high-quality sugar feedstocks has been laid; the next step will be doing it cheaper.
What challenges do you face in the work you do?
The complexity of metabolism and pathway interaction, even in an organism as well studied as our production organism, can be overwhelming. Achieving theoretical yields would be great, but is very unlikely, especially in a biological system … but, this means there will always be work to do in yield improvement. Constantly tweaking metabolism to achieve higher yields leads to very unpredictable results, which are much more often than not far from those desired. This can be challenging, and very frustrating, to deal with.
What excites you most about the work you do?
As the largest aerobic fermentation facility in the world, we are paving the way for future products and facilities. It is exciting to know that we are on the cutting edge and are leading by example down a path of sustainable manufacturing, and away from petroleum-based manufacturing.
Why do you believe sustainability/renewability matter?
Economic growth and development can only go so far on finite resources. There is a need and a push to move toward more environmentally friendly technology and industry. I think it is important to actually walk the talk in doing so, but it also puts pressure on other large manufacturing companies to do the same. This is the socially responsible reason it matters. There are also the economic factors that keep us competitive in a petroleum-heavy market. Being sustainable removes one more wild card from the game. Those in industry who do not rely on finite resources are not subject to the associated volatility of price and/or availability.
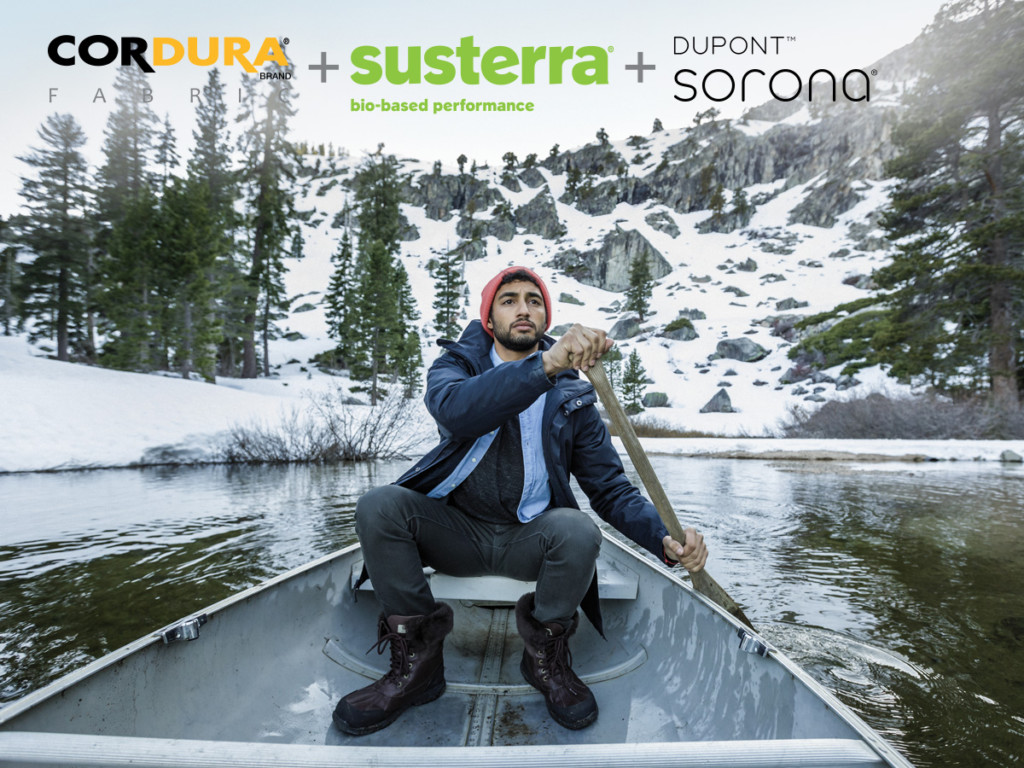
INVISTA’s CORDURA® brand, DuPont’s Sorona® brand, and DuPont Tate & Lyle’s Susterra® brand collaborated on developing a soft shell technology in part engineered from renewable sourced materials.
Interview re-issued with courtesy of DuPont Tate & Lyle. The interview was originally published here.