AIMPLAS develops biodegradable dairy packaging suitable for pasteurisation
The dairy sector will be able to package its products in biodegradable bags and bottles resistant to thermal treatments thanks to the European project BIOBOTTLE co-ordinated by AIMPLAS, Spanish research and technology center based in Valencia, Spain. The project aimed to develop a biodegradable and compostable material from which to produce both the large-sized multilayer bottles or bags used for packaging milk and the like, as well as the smaller monolayer bottles, used to package probiotic products, which are a significant source of waste in Europe. A compostable solution would eliminate the need to separate the packaging from the rest of the organic waste at the end of the product life.
AIMPLAS has now completed research and developed new biopolymers from which it will be able to manufacture new biodegradable bottles, bags and caps resistant to sterilisation and pasteurisation and has the same high standards as the currently used HDPE. The new monolayer bottles and caps and multilayer bags can resist temperatures up to 95ºC.
The BIOBOTTLE project has been developed within the European Union’s Seventh Framework Programme with a budget of one million euros. Besides AIMPLAS, companies and technology centres from Germany, Belgium Italy, Portugal, and Spain took part in the project.
FKuR launches new Bio-Flex blends that reduce the thickness of compostable films
The Bioplastic specialist FKuR has developed a new technology for the production of compounds, which can be processed into flexible packaging films with particularly low thickness and, at the same time, high puncture resistance. Films made from these new Bio-Flex® materials are suitable for food contact and compostable according to EN 13432. Depending upon the type, the bio-based content is higher than 50%. The processing of both types of blends corresponds largely to standard PE processing.
Julian Schmeling, head of development at FKuR says: “Aside from the use of renewable resources, material reduction is an essential pillar on the road to achieving greater sustainability. Films made from biodegradable resins have reached sufficient performance values with thicknesses of about 15 microns. Thanks to the use of novel polymeric additive systems and an adapted compounding process, FKuR now provides converters with the possibility to follow the trend using bioplastics and combine significant material savings along with compostability.“
Two new blends based on this new technology, Bio-Flex® FX 1120 and Bio-Flex® FX 1130, will be presented at the K 2016.
BASF offers compostable particle foam with high bio-based content
BASF is expanding its range of high performance foam products with the innovative, certified compostable particle foam ecovio® EA. The product is the first expandable, closed-cell foam material, which is predominantly biobased and certified compostable. It consists of the biodegradable BASF polymer ecoflex® and polylactic acid (PLA), which is derived from corn or other sugar-generating plants like manioc.
The properties of the patented particle foam make it particularly suitable for transport packaging for high-value or delicate goods where a high level of impact resistance and robustness is vital. The product properties are similar to those of EPS and boast energy absorption and resilience even when subjected to multiple impact loads. The high biobased content and the certified compostability make ecovio EA particularly attractive wherever fossil packaging solutions no longer meet customers’ requirements for a biobased and biodegradable transport solution.
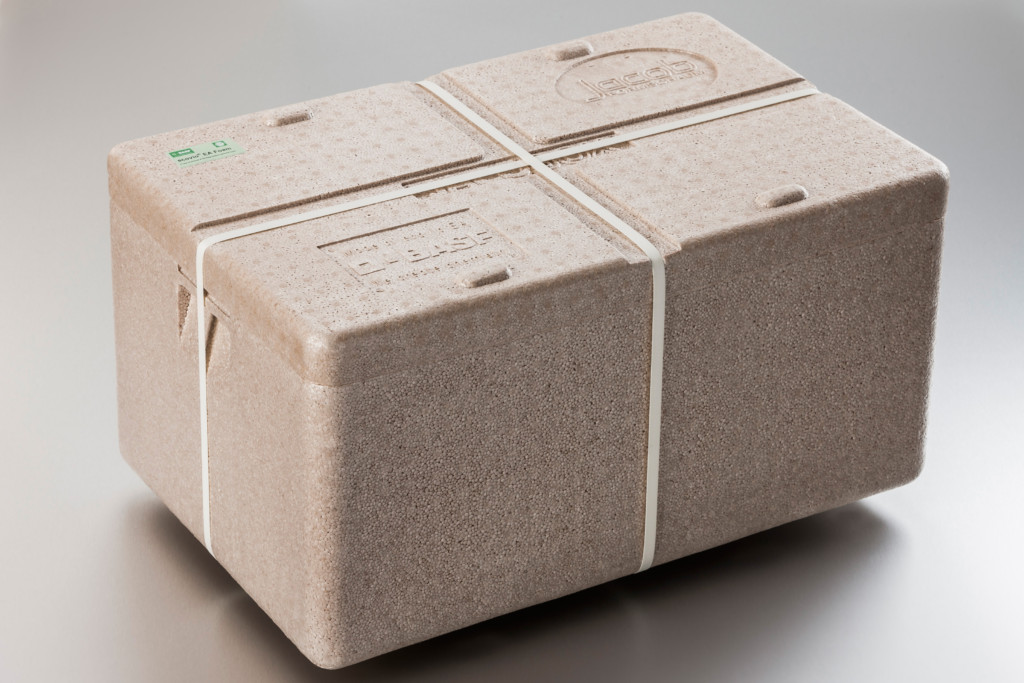
Transportation box made from BASF’s ecovio EA (c) BASF
Original Food now offers their premium wild coffee in biodegradable coffee capsules
Coffee capsules have many advantages: they allow for a practical and easy way to prepare your coffee, and they preserve the aroma and a consistent quality of every cup. But they also have a huge disadvantage: the production of the capsules, most of which contain aluminium, is very energy consuming, releases large amounts of CO2 into the atmosphere, and generates large amounts of waste that can not easily be recycled.
Freiburg-based company Original Food is a producer of premium wild coffee from sustainably sources and protected coffee fields in the Ethiopian rainforest province of Kaffa. With the growing demand in coffee capsules, the company did not want to deprive customers of its products and developed the first coffee capsule that is certified compostable according to the European standard for industrial composting EN 13432. The capsules are made entirely from PLA derived from corn or sugar cane and are suitable for Nespresso systems.
Original Food has been committed to the protection of the decimated rainforest in Ethopia by sourcing their premium, high-quality coffee from protected coffee fields in the Ethiopian rainforest province Kaffa, thus taking on a pioneering role in sustainably sourced coffee. Original Food founder Florian Hammerstein says, it was a logical step for the company to invest in the development of an ecologically sound and environmentally friendly coffee capsule.
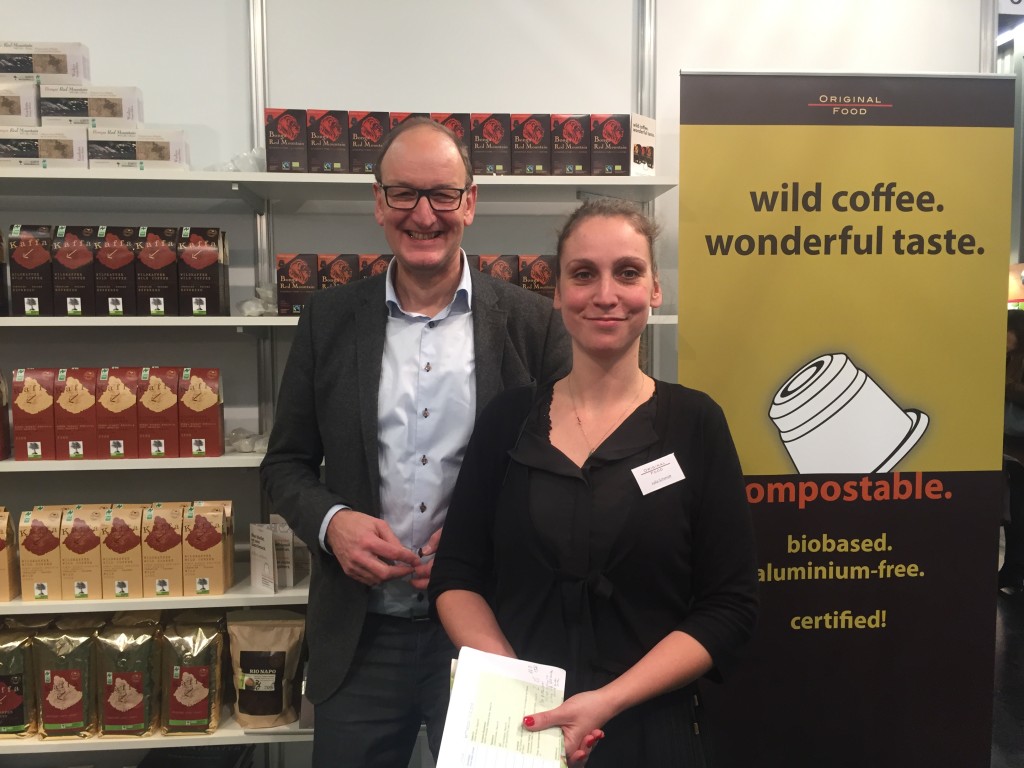
Florian Hammerstein and Julia Schmidt from Original Food at their boot at Biofach 2016